Sponsored Research
Our company is entrusted with the conception and design of heat-applied devices, as well as the proof of principle through the production of principle models.
In particular, we focus on the following technologies
- Small-scale temperature difference power generation (using Seebeck device)
- Large-scale temperature difference power generation (using rotary heat engines)
- Technology to reuse discarded hot water, etc.
- Use of radiant heat from forged products heated red hot in furnaces, etc.
- Home mist sauna device
- Mosquito coil burning dish
- liquor can machine
- Other thermal design
We have a wide range of products such as the following. We accept requests for production processing and measurement using these devices.
For more information, please contact us here.
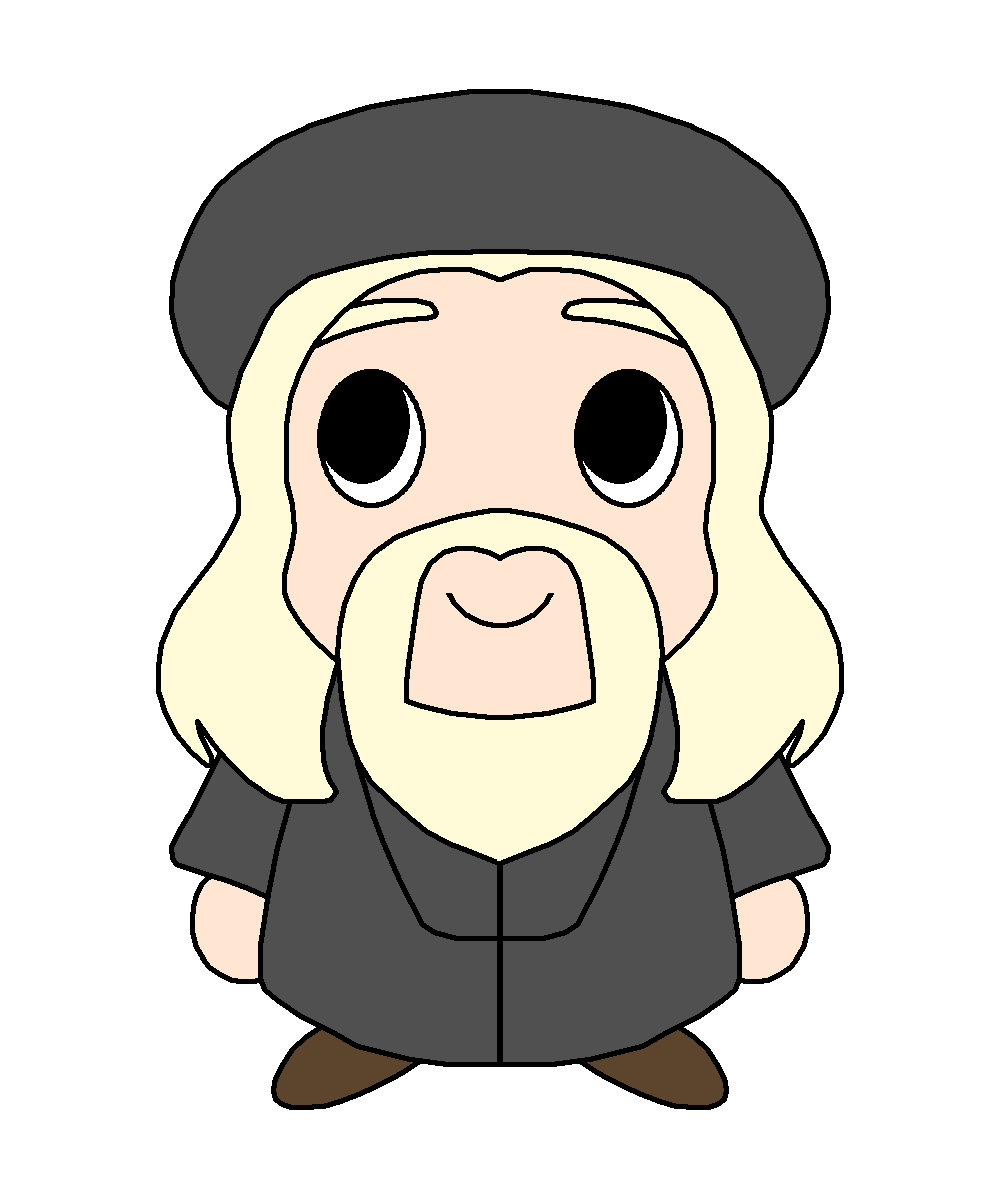
Sponsored Research
Dual Peltier Module
A Peltier device manufacturer commissioned us to establish a method of assembling a skeleton-type device, which led to the development of the Peltier device. We needed to know about semiconductors to build the device, so we investigated the Peltier and Seebeck effect.
As a result, we felt problems with the Peltier element of that time and started to develop our own. We focused on the problem of low efficiency. The main focus of our development was the development of an efficient Peltier element. We focused on the fact that Peltier elements are more efficient with less power input and worked on developing a multi-stage module.
At that time, multi-stage modules had already been commercialized by various companies. However, since they were multi-staged via a ceramic base material, the thermal resistance of the ceramic base material was large, and most modules had a large temperature difference but a small heat absorption capacity. We have developed a special thin-film bonding structure instead of ceramic for the intermediate base material. Then we have commercialized a two-stage Peltier module that can reach a maximum temperature difference of 90°C but absorb a large amount of heat. In addition, that can also be used as a power-saving type.
Dual Peltier Module
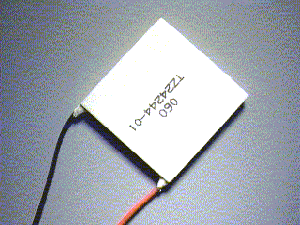
Magnetic Heat Pump
A magnetic heat pump is a device that transfers heat by using the temperature dependence of magnetic force with a magnetic liquid (magnetic fluid) as the working medium. In space, the temperature difference between the surface exposed to sunlight and the shadowed area is extremely large, and satellites are distorted by heat unless tumbling them. For this reason, transferring heat to equalize the temperature is necessary, and NASA and others have studied this. However, although the heat is transferred for a short time, it has not been possible to operate the system continuously.
The magnetic heat pump developed by our company makes use of the fact that the magnetic force of the high-temperature side of the magnetic fluid decreases when a temperature difference occurs, and the low-temperature side has a higher magnetic power. Specifically, suppose a magnet is placed in the flow path of the magnetic fluid. In that case, the low-temperature magnetic fluid will move closer to the magnet due to the difference in magnetization value, and the high-temperature magnetic fluid will move away from the magnet. Due to this effect, the magnetic fluid with higher temperatures is continuously driven away from the magnetic field by the magnetic fluid with lower temperatures. When a magnetic heat pump is placed over a heating element and a heat sink, the magnetic fluid heated in the heating element is pushed out of the magnetic field by the magnetic liquid cooled in the heat sink. Then the heat of the heating element can be transferred continuously to the heat sink. *Patent registered. There are references(no English version).
Magnetic Heat Pump
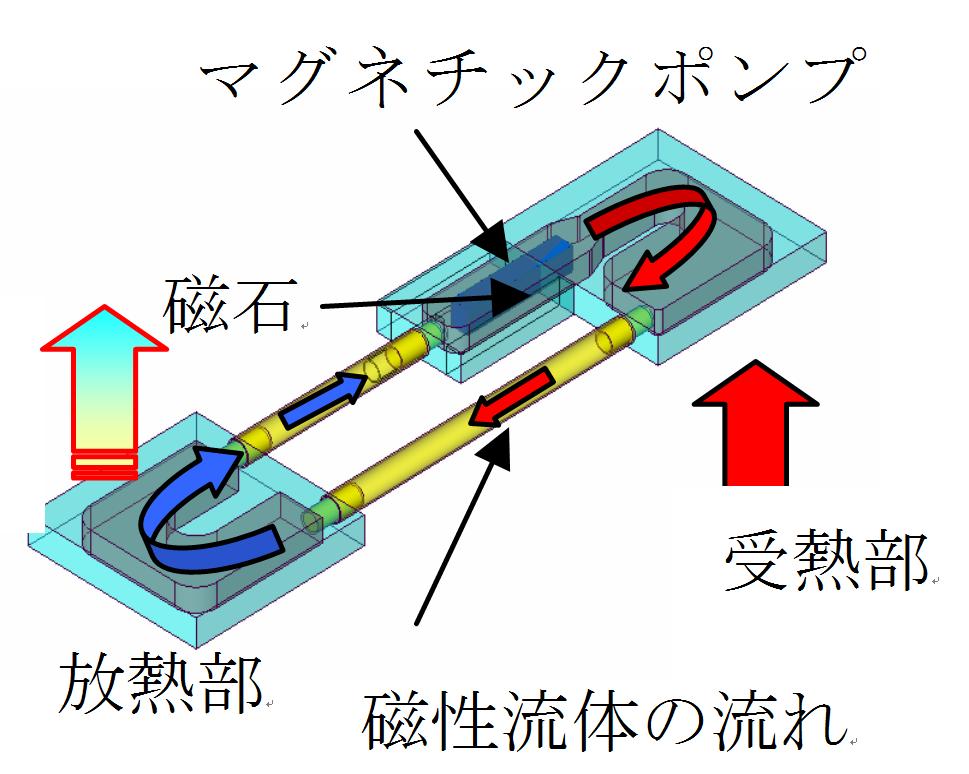
Seebeck Devices
We were commissioned to develop a Seebeck module by an electric power company. We worked with several companies to build a module with high thermoelectric conversion efficiency at low temperatures. We proposed a structure in which an insulating layer is sandwiched between the junction of P-type and N-type semiconductors. Originally, Seebeck modules had almost the same structure as solar cells. The significant difference was that the I-layer of neutral semiconductors was sandwiched between the P-type and N-type semiconductors.
The inspiration for the development came from a story I heard when I was a co-researcher in the Nakasuka Laboratory of the Department of Aeronautics and Astronautics, Graduate School of Engineering, the University of Tokyo. When a solar cell reaches the end of its life in space, it may show high efficiency for a moment and then break down. I hypothesized that this was due to a vacuum gap of a few ㎛ in the I-layer connecting the P-type and N-type semiconductors, which created a flow of electrons like a discharge in a vacuum.
In the experiment with a 20㎛ insulating layer between the P-type semiconductor and the electrode in the Seebeck module, the electromotive force was generated at a temperature difference of about 30℃. When the insulating layer was thickened to 50㎛, the electromotive force was generated at a temperature difference of about 75℃, and the module behaved like a temperature switch. In this case, the voltage of the electromotive force was high, and the current increased accordingly. We have succeeded in developing a prototype Seebeck module with high efficiency even at low temperatures. Still, we are holding off on commercializing it on our own due to equipment and other problems. *Patent registered.
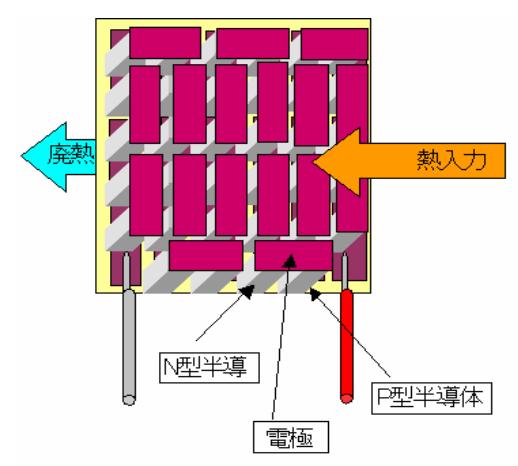
Seebeck Devices